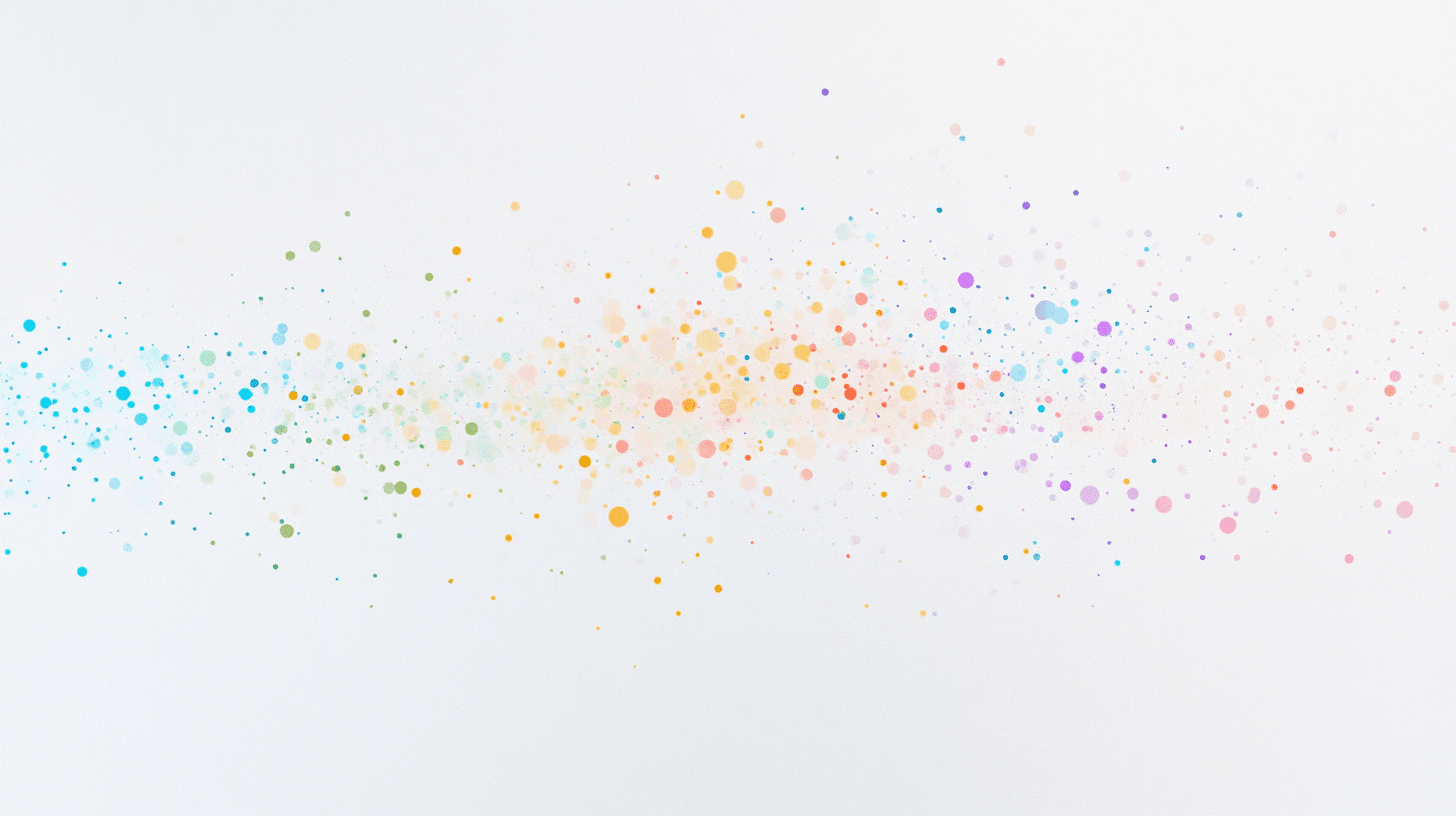
Our Work
Explore recent projects completed by iSOS.

Database Development
Highway Index
Highway Index is a free online directory that provides detailed information on companies and local authorities operating within the UK’s highway electrical and maintenance sectors. It serves as a central resource for industry professionals, offering access to company profiles, local authority contacts, and contract details relevant to the highway industry.

Database Development
Highway Index
Highway Index is a free online directory that provides detailed information on companies and local authorities operating within the UK’s highway electrical and maintenance sectors. It serves as a central resource for industry professionals, offering access to company profiles, local authority contacts, and contract details relevant to the highway industry.

Database Development
Highway Index
Highway Index is a free online directory that provides detailed information on companies and local authorities operating within the UK’s highway electrical and maintenance sectors. It serves as a central resource for industry professionals, offering access to company profiles, local authority contacts, and contract details relevant to the highway industry.

Database Development
David Nash
David Nash, a distinguished British sculptor celebrated for his work with wood, trees, and the natural environment, needed a robust system to efficiently manage his vast sculpture catalog, global gallery partnerships, and studio operations.

Database Development
David Nash
David Nash, a distinguished British sculptor celebrated for his work with wood, trees, and the natural environment, needed a robust system to efficiently manage his vast sculpture catalog, global gallery partnerships, and studio operations.

Database Development
David Nash
David Nash, a distinguished British sculptor celebrated for his work with wood, trees, and the natural environment, needed a robust system to efficiently manage his vast sculpture catalog, global gallery partnerships, and studio operations.
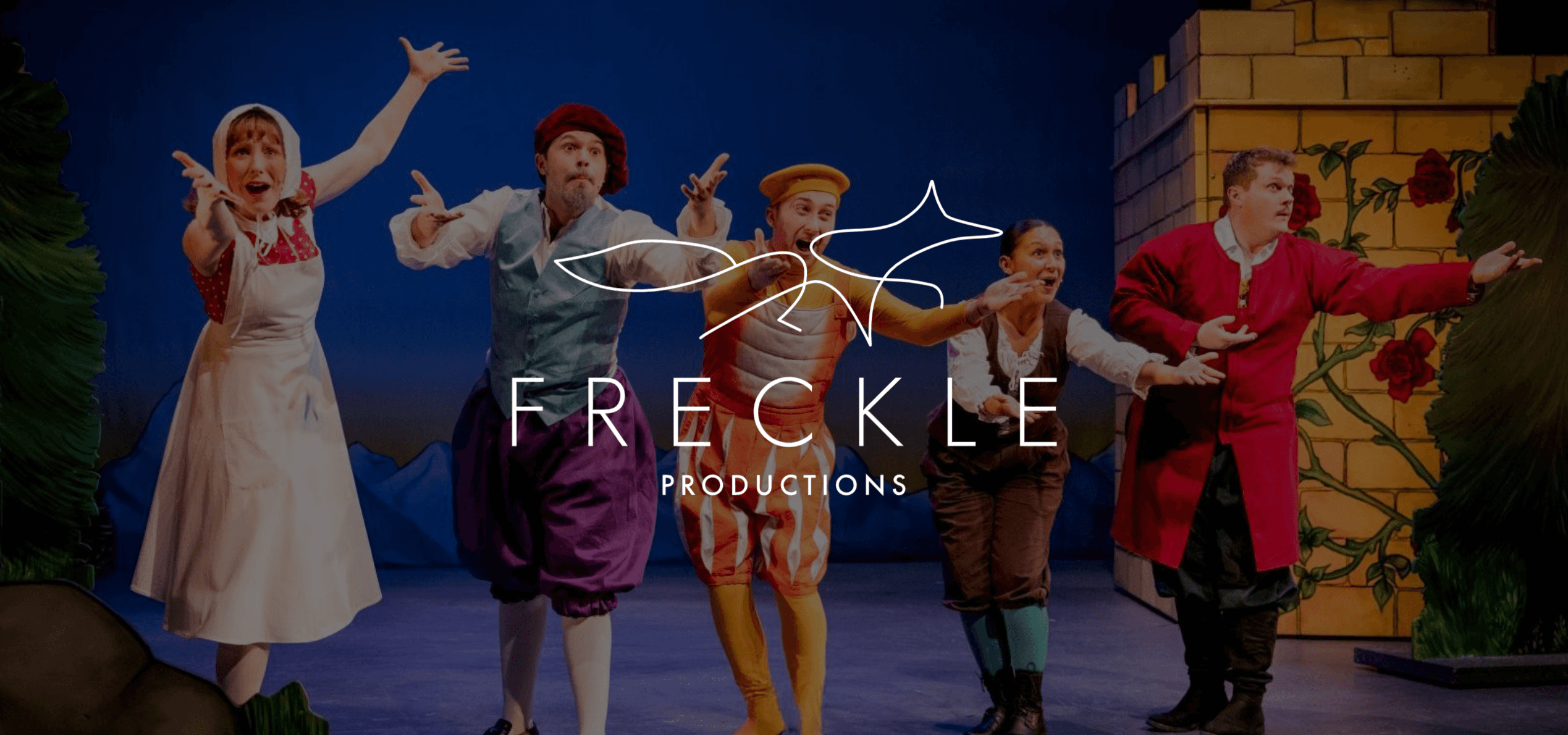
Database Development
Freckle Productions
To support their expansion, Freckle Productions implemented a bespoke Claris FileMaker database solution that centralises operations, optimises tour scheduling, and enhances financial management. This comprehensive system delivers real-time insights and planning capabilities, elevating their already successful theatre production process.
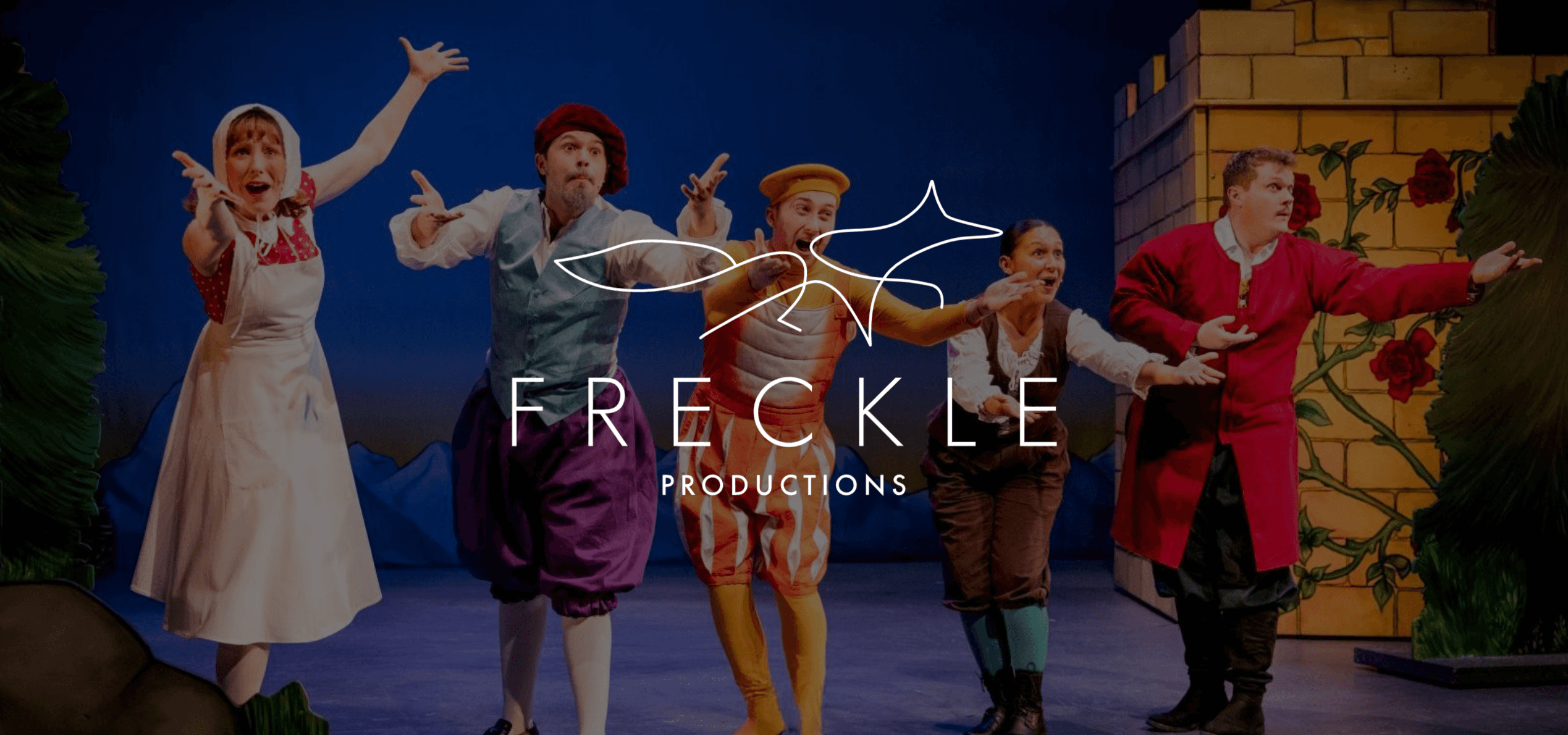
Database Development
Freckle Productions
To support their expansion, Freckle Productions implemented a bespoke Claris FileMaker database solution that centralises operations, optimises tour scheduling, and enhances financial management. This comprehensive system delivers real-time insights and planning capabilities, elevating their already successful theatre production process.
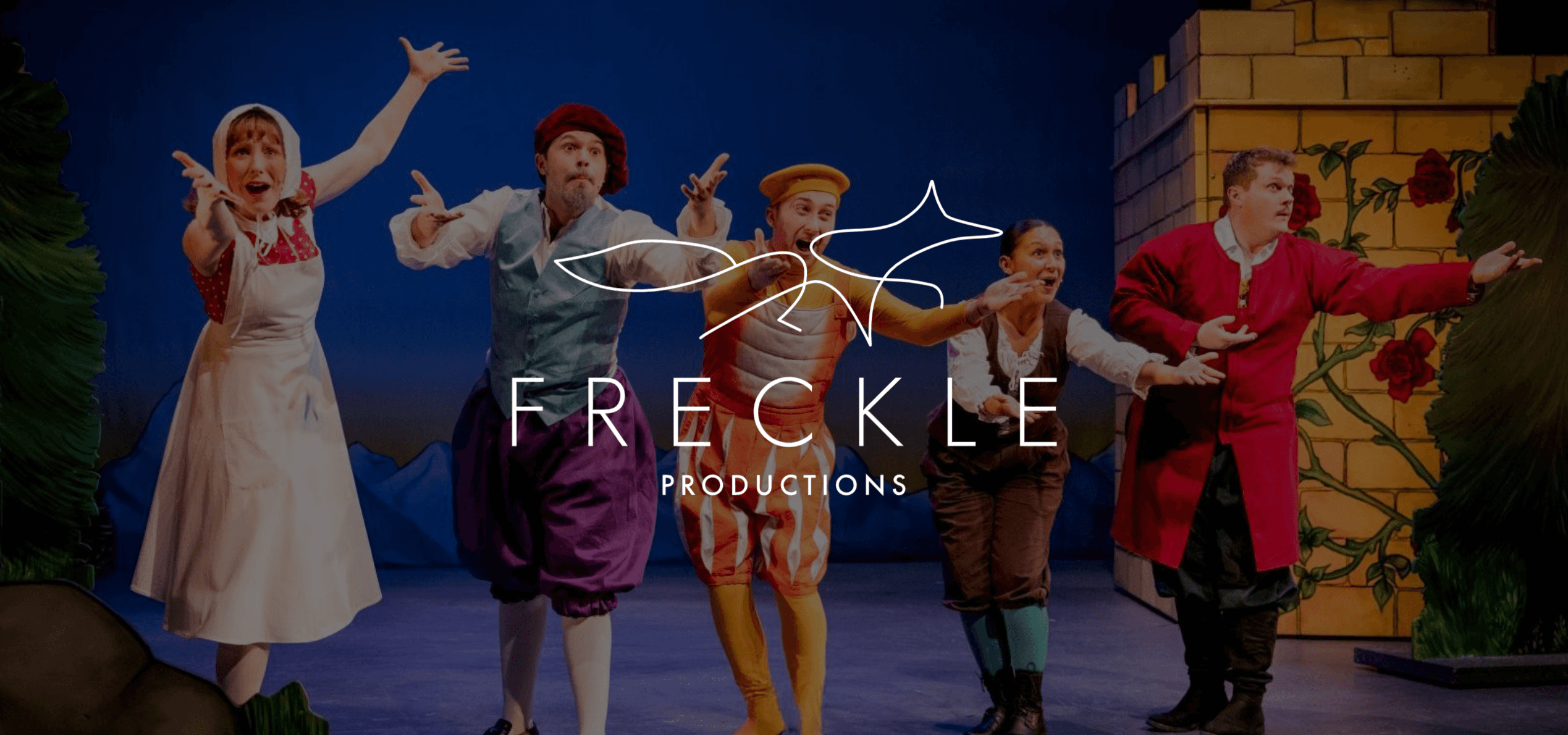
Database Development
Freckle Productions
To support their expansion, Freckle Productions implemented a bespoke Claris FileMaker database solution that centralises operations, optimises tour scheduling, and enhances financial management. This comprehensive system delivers real-time insights and planning capabilities, elevating their already successful theatre production process.

Database Development
Learning Resources for Schools
A leading UK educational services provider faced challenges as it expanded, with existing systems struggling to manage complexity. They partnered with iSOS to implement a bespoke Claris FileMaker solution, streamlining operations from enquiries to logistics and invoicing.

Database Development
Learning Resources for Schools
A leading UK educational services provider faced challenges as it expanded, with existing systems struggling to manage complexity. They partnered with iSOS to implement a bespoke Claris FileMaker solution, streamlining operations from enquiries to logistics and invoicing.

Database Development
Learning Resources for Schools
A leading UK educational services provider faced challenges as it expanded, with existing systems struggling to manage complexity. They partnered with iSOS to implement a bespoke Claris FileMaker solution, streamlining operations from enquiries to logistics and invoicing.
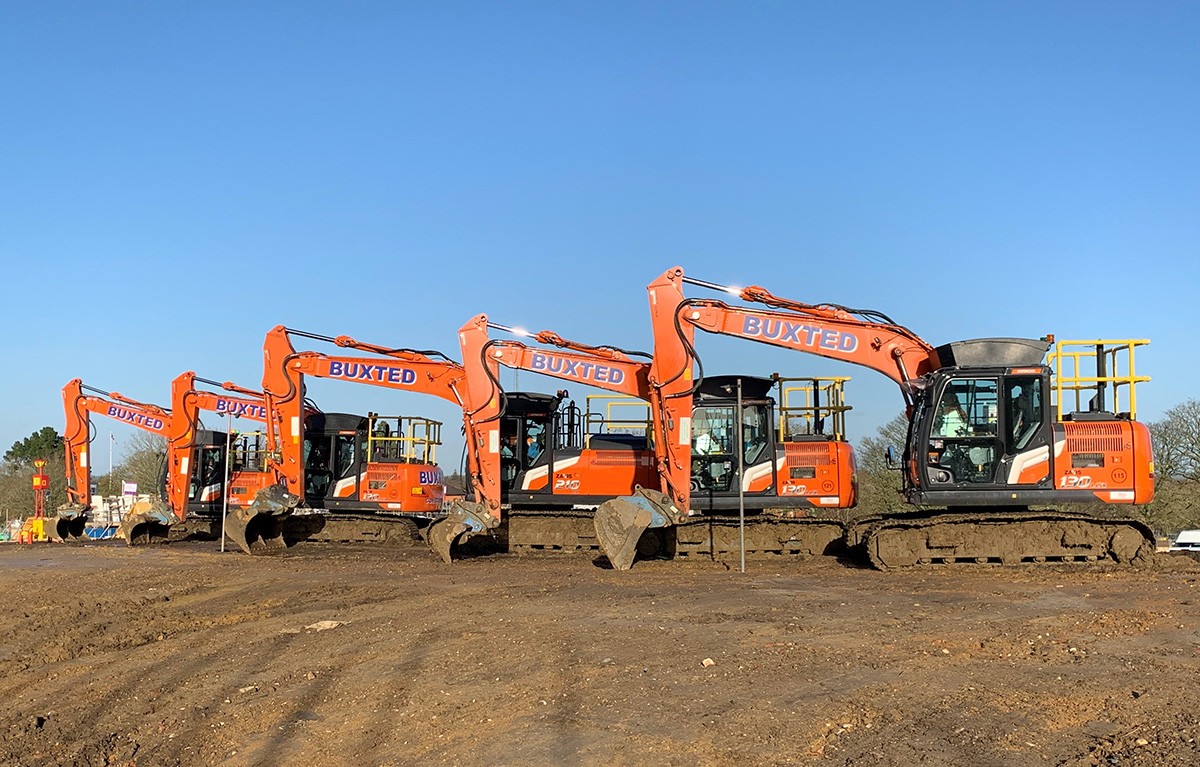
App Development
Buxted Construction
Buxted Construction, a firm specialising in groundworks and civil engineering, struggled with manual, paper-based timesheets. With around 415 operatives across multiple sites, this system caused errors and delays. The company needed a more efficient, accurate solution for workforce management and asset tracking.
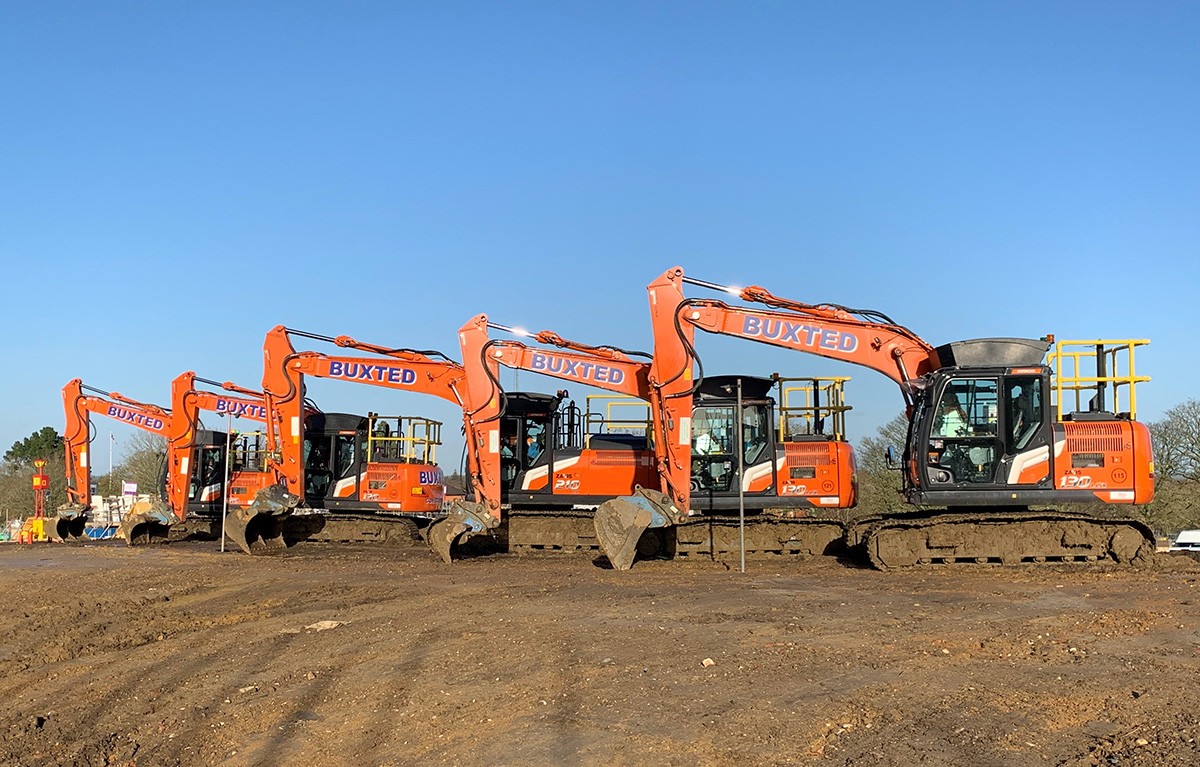
App Development
Buxted Construction
Buxted Construction, a firm specialising in groundworks and civil engineering, struggled with manual, paper-based timesheets. With around 415 operatives across multiple sites, this system caused errors and delays. The company needed a more efficient, accurate solution for workforce management and asset tracking.
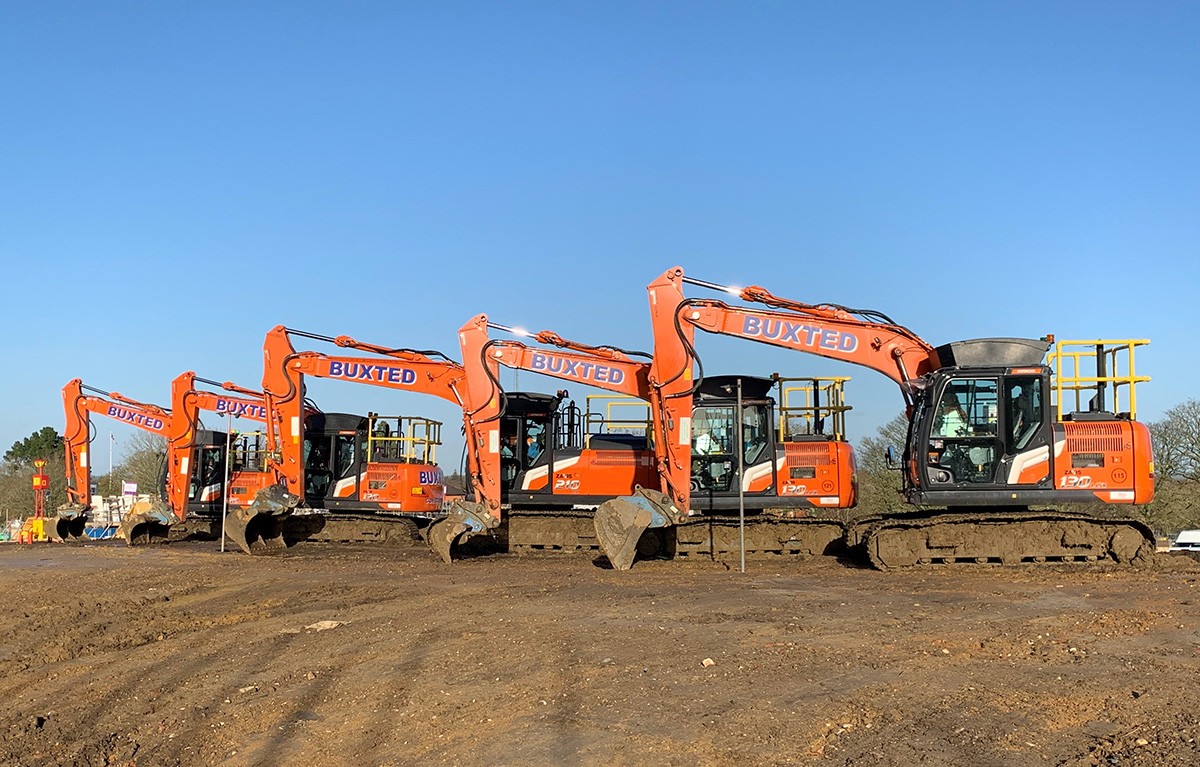
App Development
Buxted Construction
Buxted Construction, a firm specialising in groundworks and civil engineering, struggled with manual, paper-based timesheets. With around 415 operatives across multiple sites, this system caused errors and delays. The company needed a more efficient, accurate solution for workforce management and asset tracking.

Web Development
Quentin Blake
Sir Quentin Blake sought a new website with the goal of enhancing user engagement, facing two main challenges: improving technical aspects like responsiveness and navigation for a seamless user experience, and integrating his unique artistic style into every design element to create a vivid online presence.

Web Development
Quentin Blake
Sir Quentin Blake sought a new website with the goal of enhancing user engagement, facing two main challenges: improving technical aspects like responsiveness and navigation for a seamless user experience, and integrating his unique artistic style into every design element to create a vivid online presence.

Web Development
Quentin Blake
Sir Quentin Blake sought a new website with the goal of enhancing user engagement, facing two main challenges: improving technical aspects like responsiveness and navigation for a seamless user experience, and integrating his unique artistic style into every design element to create a vivid online presence.

Web & Database Development
Chris Beetles
The aim was to develop a new website focusing on images to highlight the gallery's art collection. After consulting, we decided to rebuild the site using the Laravel framework and also redevelop the FileMaker database to integrate with this new platform.

Web & Database Development
Chris Beetles
The aim was to develop a new website focusing on images to highlight the gallery's art collection. After consulting, we decided to rebuild the site using the Laravel framework and also redevelop the FileMaker database to integrate with this new platform.

Web & Database Development
Chris Beetles
The aim was to develop a new website focusing on images to highlight the gallery's art collection. After consulting, we decided to rebuild the site using the Laravel framework and also redevelop the FileMaker database to integrate with this new platform.

Database Development
Bromptons Opticians
The Bromptons Opticians case study showcases how iSOS enhanced the business by implementing custom digital solutions. It details how tailored IT services streamlined operations, improved efficiency, and supported overall growth.

Database Development
Bromptons Opticians
The Bromptons Opticians case study showcases how iSOS enhanced the business by implementing custom digital solutions. It details how tailored IT services streamlined operations, improved efficiency, and supported overall growth.

Database Development
Bromptons Opticians
The Bromptons Opticians case study showcases how iSOS enhanced the business by implementing custom digital solutions. It details how tailored IT services streamlined operations, improved efficiency, and supported overall growth.

Database Development
Autumn Lodge
The Autumn Lodge case study highlights how iSOS implemented customised digital solutions to enhance the care home's operations. The study details how these solutions improved efficiency, streamlined processes, and supported better care delivery for residents.

Database Development
Autumn Lodge
The Autumn Lodge case study highlights how iSOS implemented customised digital solutions to enhance the care home's operations. The study details how these solutions improved efficiency, streamlined processes, and supported better care delivery for residents.

Database Development
Autumn Lodge
The Autumn Lodge case study highlights how iSOS implemented customised digital solutions to enhance the care home's operations. The study details how these solutions improved efficiency, streamlined processes, and supported better care delivery for residents.

Database Development
BCM Public Relations
The BCM Public Relations case study details how iSOS implemented tailored digital solutions to streamline the agency's operations. It highlights improvements in efficiency, workflow management, and service delivery, ultimately enhancing BCM's ability to serve its clients more effectively.

Database Development
BCM Public Relations
The BCM Public Relations case study details how iSOS implemented tailored digital solutions to streamline the agency's operations. It highlights improvements in efficiency, workflow management, and service delivery, ultimately enhancing BCM's ability to serve its clients more effectively.

Database Development
BCM Public Relations
The BCM Public Relations case study details how iSOS implemented tailored digital solutions to streamline the agency's operations. It highlights improvements in efficiency, workflow management, and service delivery, ultimately enhancing BCM's ability to serve its clients more effectively.

Web Development
Morgan Classic Wines
The Morgan Classic Wines case study showcases how iSOS implemented tailored digital solutions to enhance the wine retailer's operations. The study details improvements in efficiency, inventory management, and customer experience, helping the business to better serve its clientele.

Web Development
Morgan Classic Wines
The Morgan Classic Wines case study showcases how iSOS implemented tailored digital solutions to enhance the wine retailer's operations. The study details improvements in efficiency, inventory management, and customer experience, helping the business to better serve its clientele.

Web Development
Morgan Classic Wines
The Morgan Classic Wines case study showcases how iSOS implemented tailored digital solutions to enhance the wine retailer's operations. The study details improvements in efficiency, inventory management, and customer experience, helping the business to better serve its clientele.
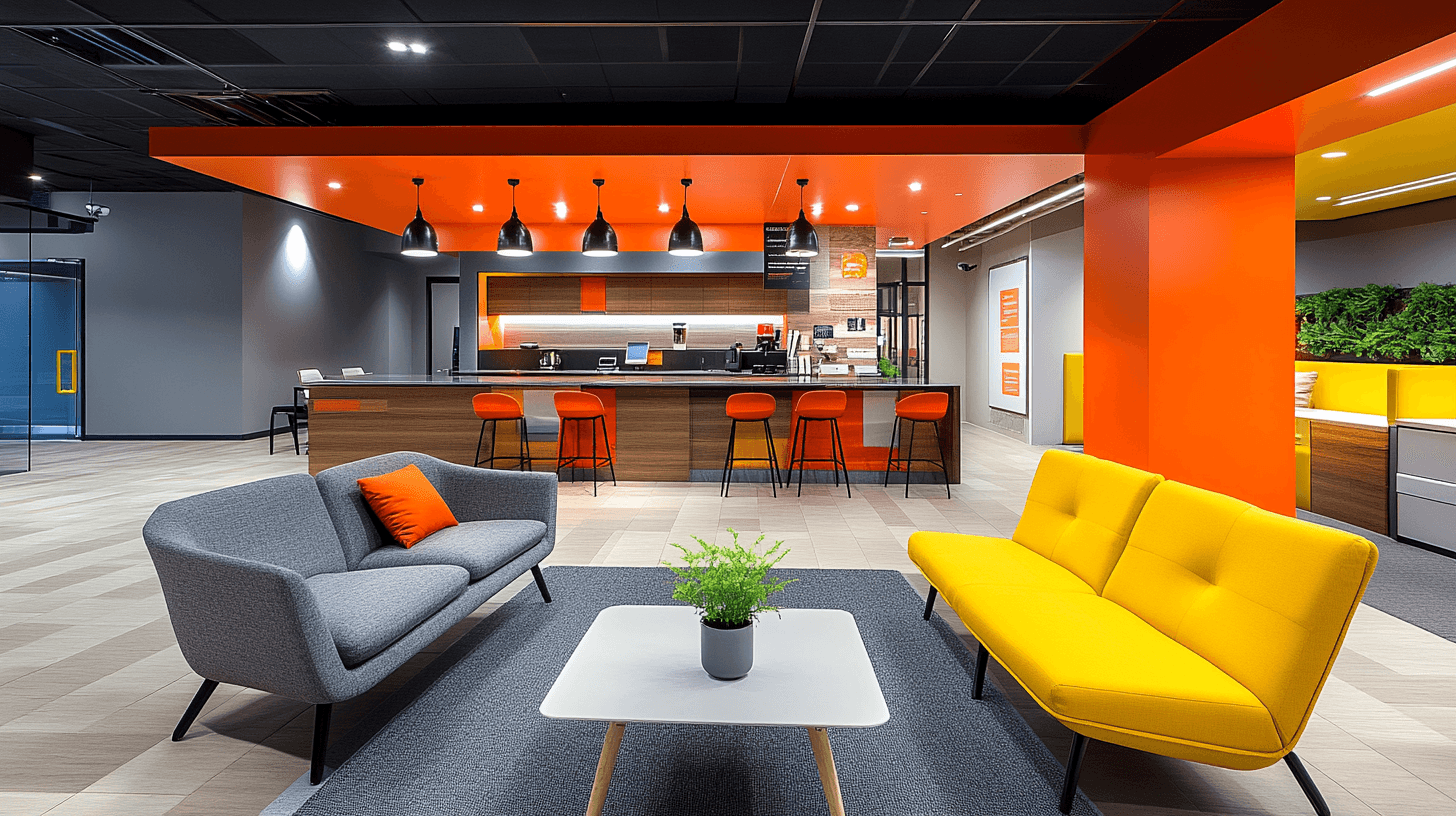
Web Development
Gearing Media Group
The Gearing Media Group case study details how iSOS implemented digital solutions to optimise the media company's operations. The study covers enhancements in workflow management, efficiency, and overall productivity, enabling the company to better manage its media projects.
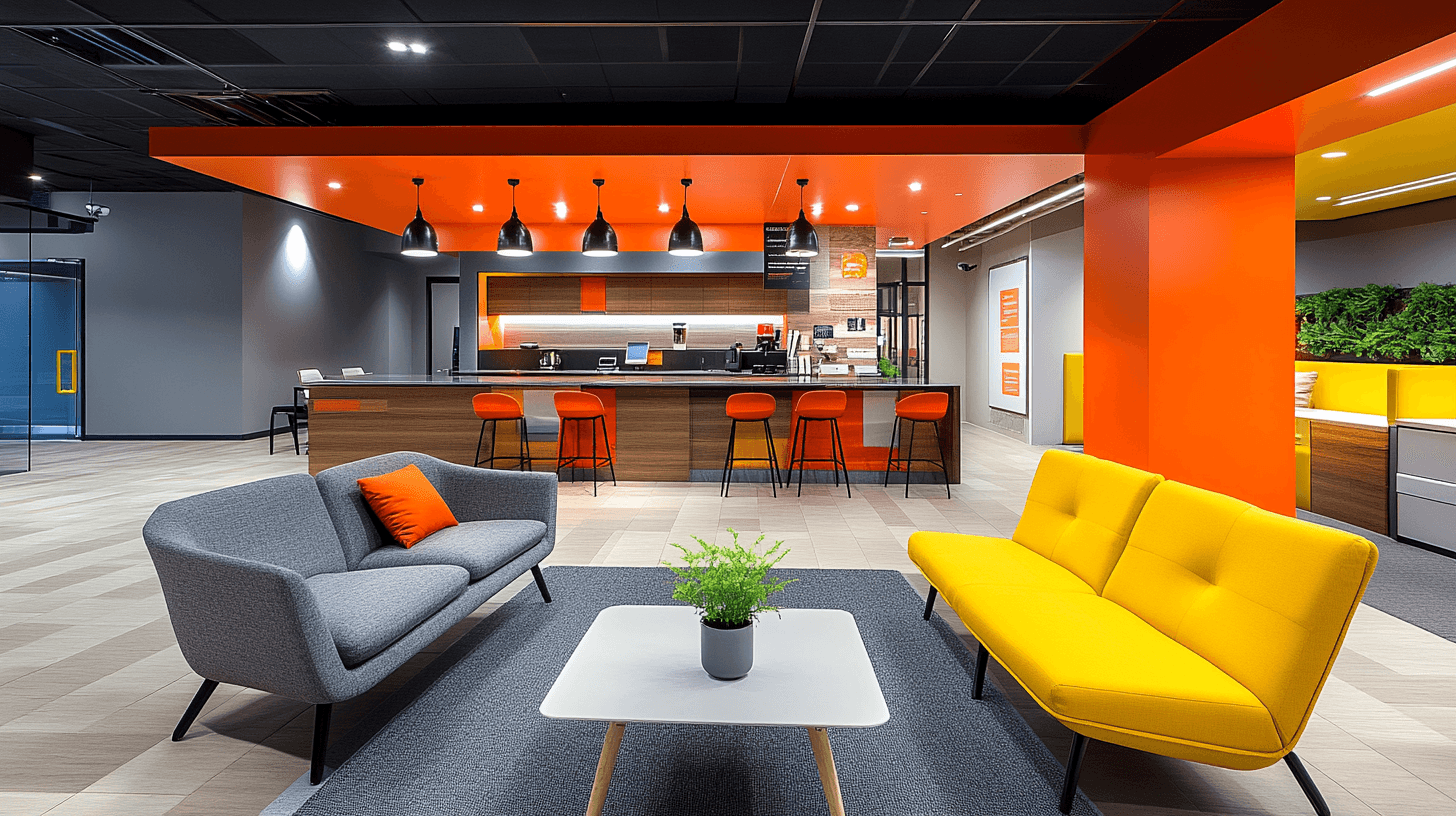
Web Development
Gearing Media Group
The Gearing Media Group case study details how iSOS implemented digital solutions to optimise the media company's operations. The study covers enhancements in workflow management, efficiency, and overall productivity, enabling the company to better manage its media projects.
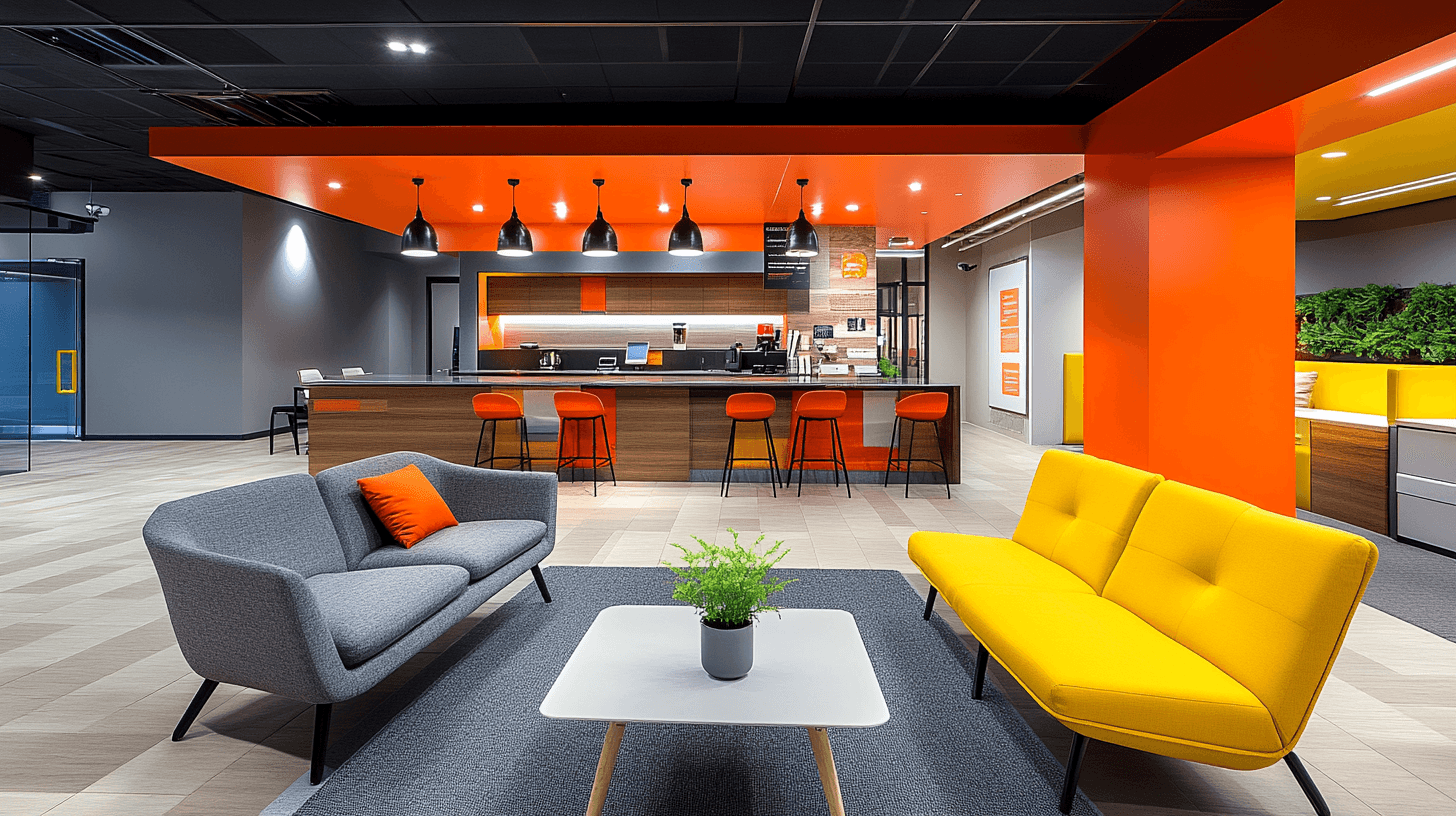
Web Development
Gearing Media Group
The Gearing Media Group case study details how iSOS implemented digital solutions to optimise the media company's operations. The study covers enhancements in workflow management, efficiency, and overall productivity, enabling the company to better manage its media projects.

Web Development
Human Givens Institute
The Human Givens Institute case study focuses on how iSOS developed custom digital solutions to streamline their educational services. We implemented an improved online learning management system, enhanced user experience, and optimised operational efficiency, helping the institute better deliver its mental health training programmes.

Web Development
Human Givens Institute
The Human Givens Institute case study focuses on how iSOS developed custom digital solutions to streamline their educational services. We implemented an improved online learning management system, enhanced user experience, and optimised operational efficiency, helping the institute better deliver its mental health training programmes.

Web Development
Human Givens Institute
The Human Givens Institute case study focuses on how iSOS developed custom digital solutions to streamline their educational services. We implemented an improved online learning management system, enhanced user experience, and optimised operational efficiency, helping the institute better deliver its mental health training programmes.
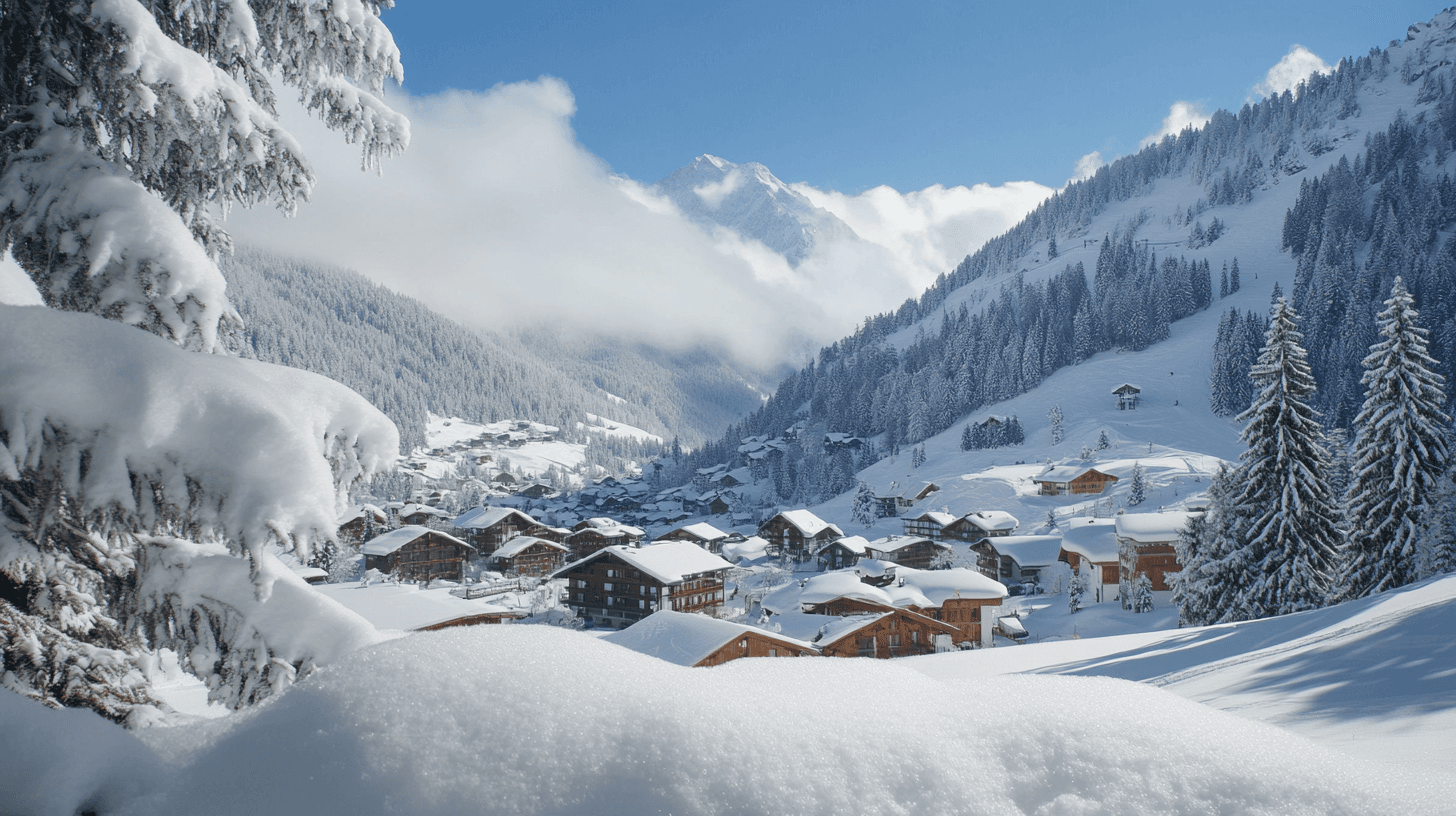
Database Development
Mountain Spaces
The Mountain Spaces case study outlines how iSOS developed tailored digital solutions to enhance the travel company's operations. We improved their booking systems, streamlined business processes, and optimised customer experience, helping Mountain Spaces provide a more efficient and user-friendly service for their clients.
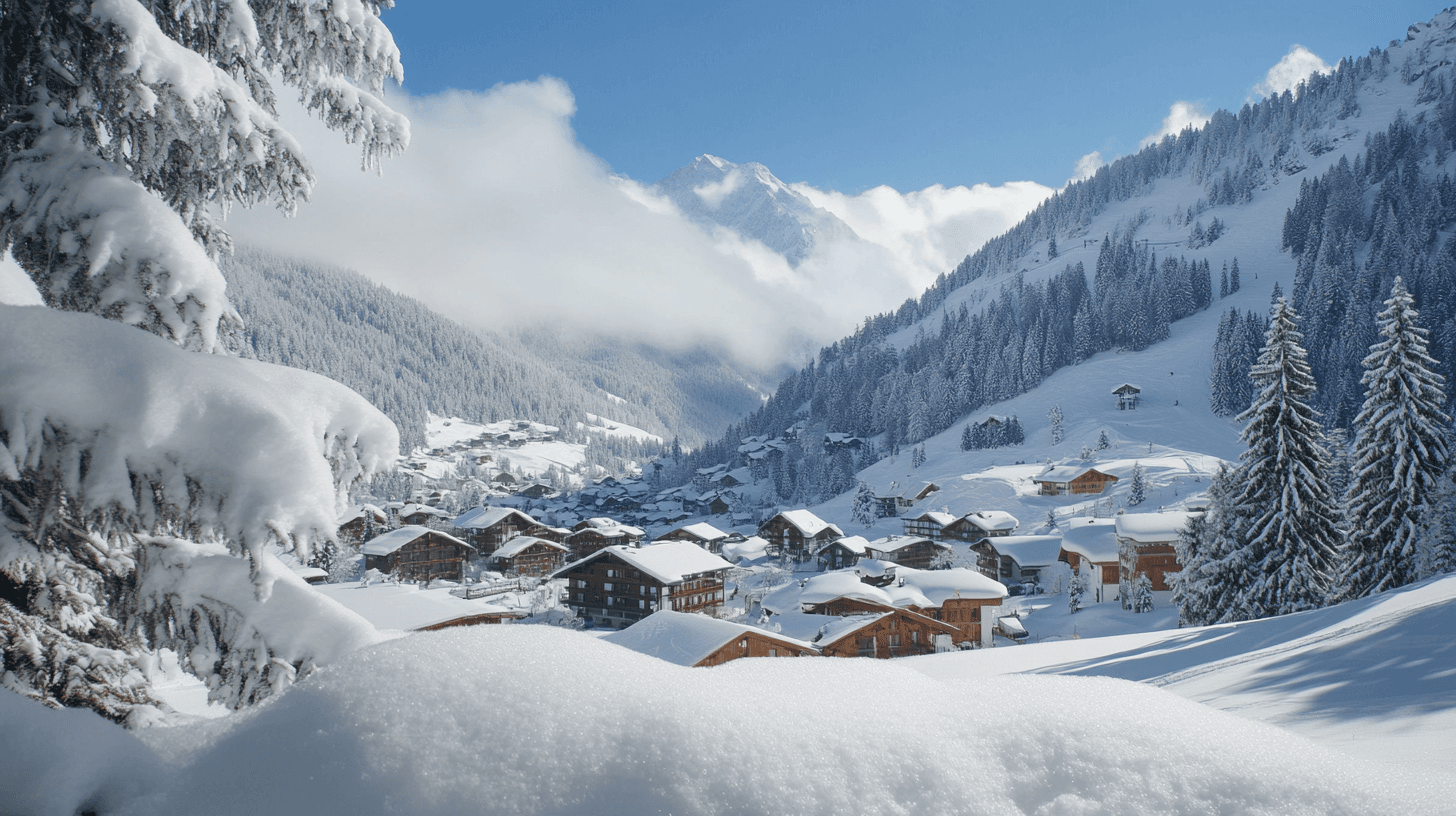
Database Development
Mountain Spaces
The Mountain Spaces case study outlines how iSOS developed tailored digital solutions to enhance the travel company's operations. We improved their booking systems, streamlined business processes, and optimised customer experience, helping Mountain Spaces provide a more efficient and user-friendly service for their clients.
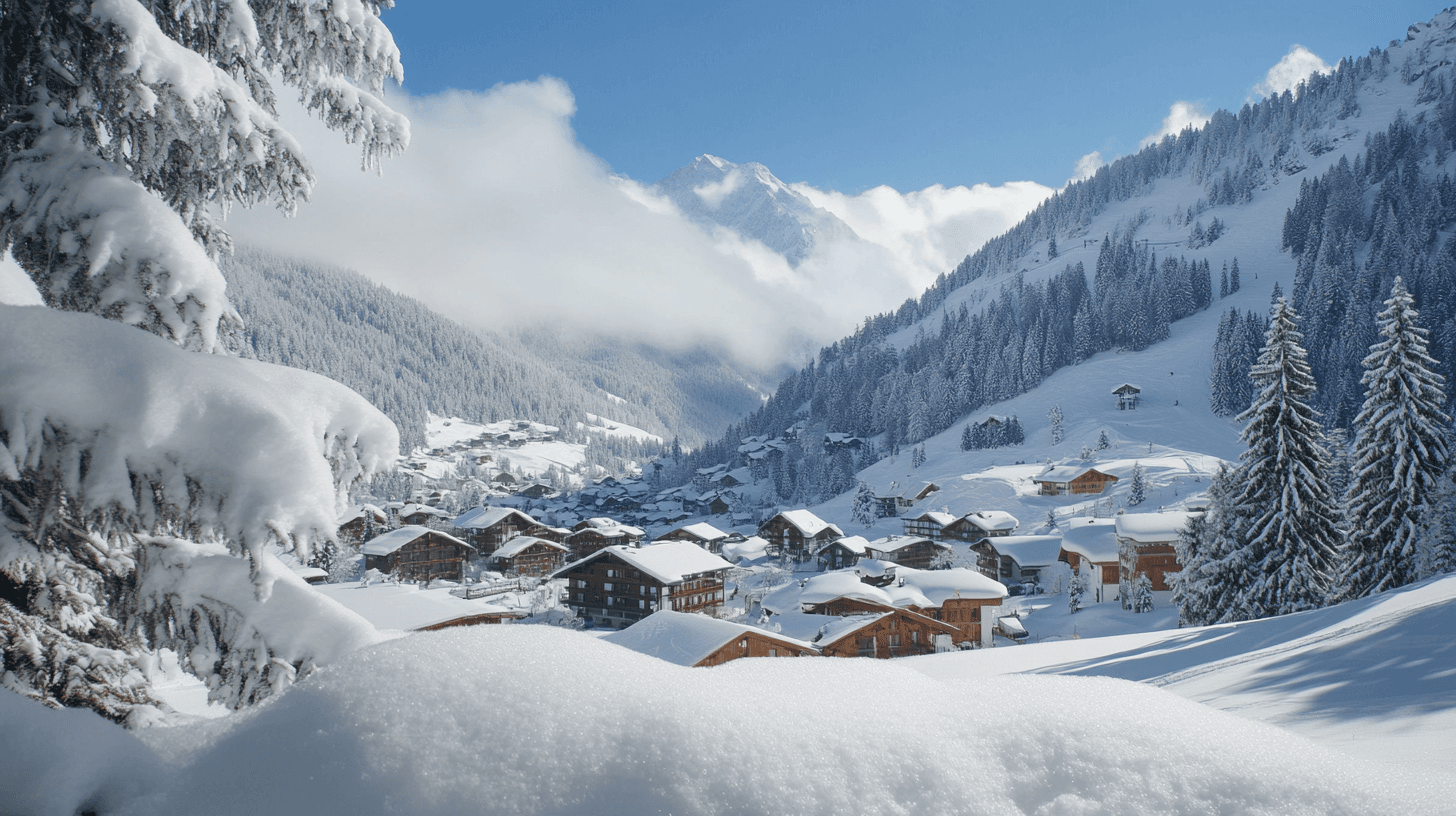
Database Development
Mountain Spaces
The Mountain Spaces case study outlines how iSOS developed tailored digital solutions to enhance the travel company's operations. We improved their booking systems, streamlined business processes, and optimised customer experience, helping Mountain Spaces provide a more efficient and user-friendly service for their clients.

Database Development
Milborrow Chimney Sweeps
The Milborrow Chimney Sweeps case study showcases how iSOS implemented digital solutions to modernise the company's operations. We developed a tailored system to improve scheduling, enhance customer management, and streamline business processes, enabling Milborrow Chimney Sweeps to operate more efficiently while maintaining high service standards.

Database Development
Milborrow Chimney Sweeps
The Milborrow Chimney Sweeps case study showcases how iSOS implemented digital solutions to modernise the company's operations. We developed a tailored system to improve scheduling, enhance customer management, and streamline business processes, enabling Milborrow Chimney Sweeps to operate more efficiently while maintaining high service standards.

Database Development
Milborrow Chimney Sweeps
The Milborrow Chimney Sweeps case study showcases how iSOS implemented digital solutions to modernise the company's operations. We developed a tailored system to improve scheduling, enhance customer management, and streamline business processes, enabling Milborrow Chimney Sweeps to operate more efficiently while maintaining high service standards.
Solutions we use
Clients Feedback
How Our Digital Solutions Transformed Businesses
"iSOS listened to our brief and our needs and were able to provide us with advice, suggestions as to how to structure the solution and eventually an accurate, detailed quote that didn’t change during the entire process. The solution was delivered on time and on budget."
Mountain Spaces
"Heritage Collective approached iSOS to develop a bespoke database system. We’ve been very pleased with the result and they’ve been a great team to work with. Methodical and approachable, they took the time to understand our business and encouraged regular engagement which led to a tailor-made product that hit the spot."
Heritage Collective
"I would like to say thank you for delivering such a great application so quickly and professionally. I was very impressed with the way that the team had gone through the documentation before the project brief, and had all of the right questions ready for us."
Eazy Collect
"Our experience through iSOS has been 5*, and the continued support from iSOS on very rare glitches (inevitable in the moving world of IT) is well managed"
Buxted Construction
"The iSOS team helped us to create a database for our production company. The entire process from start to finish was very straightforward and they took great care to explain every step and worked very hard to give us a finished product which was tailor-made to our needs."
Freckle Productions
"“This was our first major FileMaker project. Working with iSOS has been a good collaborative experience, and the majority of the work has been done remotely. The benefit of a fully customised system is that we can continue to improve the way it works to precisely fit the needs of our business."
Learning Resources for Schools
"iSOS listened to our brief and our needs and were able to provide us with advice, suggestions as to how to structure the solution and eventually an accurate, detailed quote that didn’t change during the entire process. The solution was delivered on time and on budget."
Mountain Spaces
"Heritage Collective approached iSOS to develop a bespoke database system. We’ve been very pleased with the result and they’ve been a great team to work with. Methodical and approachable, they took the time to understand our business and encouraged regular engagement which led to a tailor-made product that hit the spot."
Heritage Collective
"I would like to say thank you for delivering such a great application so quickly and professionally. I was very impressed with the way that the team had gone through the documentation before the project brief, and had all of the right questions ready for us."
Eazy Collect
"Our experience through iSOS has been 5*, and the continued support from iSOS on very rare glitches (inevitable in the moving world of IT) is well managed"
Buxted Construction
"The iSOS team helped us to create a database for our production company. The entire process from start to finish was very straightforward and they took great care to explain every step and worked very hard to give us a finished product which was tailor-made to our needs."
Freckle Productions
"“This was our first major FileMaker project. Working with iSOS has been a good collaborative experience, and the majority of the work has been done remotely. The benefit of a fully customised system is that we can continue to improve the way it works to precisely fit the needs of our business."
Learning Resources for Schools
"iSOS listened to our brief and our needs and were able to provide us with advice, suggestions as to how to structure the solution and eventually an accurate, detailed quote that didn’t change during the entire process. The solution was delivered on time and on budget."
Mountain Spaces
"Heritage Collective approached iSOS to develop a bespoke database system. We’ve been very pleased with the result and they’ve been a great team to work with. Methodical and approachable, they took the time to understand our business and encouraged regular engagement which led to a tailor-made product that hit the spot."
Heritage Collective
"I would like to say thank you for delivering such a great application so quickly and professionally. I was very impressed with the way that the team had gone through the documentation before the project brief, and had all of the right questions ready for us."
Eazy Collect
"Our experience through iSOS has been 5*, and the continued support from iSOS on very rare glitches (inevitable in the moving world of IT) is well managed"
Buxted Construction
"The iSOS team helped us to create a database for our production company. The entire process from start to finish was very straightforward and they took great care to explain every step and worked very hard to give us a finished product which was tailor-made to our needs."
Freckle Productions
"“This was our first major FileMaker project. Working with iSOS has been a good collaborative experience, and the majority of the work has been done remotely. The benefit of a fully customised system is that we can continue to improve the way it works to precisely fit the needs of our business."
Learning Resources for Schools
"iSOS listened to our brief and our needs and were able to provide us with advice, suggestions as to how to structure the solution and eventually an accurate, detailed quote that didn’t change during the entire process. The solution was delivered on time and on budget."
Mountain Spaces
"Heritage Collective approached iSOS to develop a bespoke database system. We’ve been very pleased with the result and they’ve been a great team to work with. Methodical and approachable, they took the time to understand our business and encouraged regular engagement which led to a tailor-made product that hit the spot."
Heritage Collective
"I would like to say thank you for delivering such a great application so quickly and professionally. I was very impressed with the way that the team had gone through the documentation before the project brief, and had all of the right questions ready for us."
Eazy Collect
"Our experience through iSOS has been 5*, and the continued support from iSOS on very rare glitches (inevitable in the moving world of IT) is well managed"
Buxted Construction
"The iSOS team helped us to create a database for our production company. The entire process from start to finish was very straightforward and they took great care to explain every step and worked very hard to give us a finished product which was tailor-made to our needs."
Freckle Productions
"“This was our first major FileMaker project. Working with iSOS has been a good collaborative experience, and the majority of the work has been done remotely. The benefit of a fully customised system is that we can continue to improve the way it works to precisely fit the needs of our business."
Learning Resources for Schools
"iSOS listened to our brief and our needs and were able to provide us with advice, suggestions as to how to structure the solution and eventually an accurate, detailed quote that didn’t change during the entire process. The solution was delivered on time and on budget."
Mountain Spaces
"Heritage Collective approached iSOS to develop a bespoke database system. We’ve been very pleased with the result and they’ve been a great team to work with. Methodical and approachable, they took the time to understand our business and encouraged regular engagement which led to a tailor-made product that hit the spot."
Heritage Collective
"I would like to say thank you for delivering such a great application so quickly and professionally. I was very impressed with the way that the team had gone through the documentation before the project brief, and had all of the right questions ready for us."
Eazy Collect
"Our experience through iSOS has been 5*, and the continued support from iSOS on very rare glitches (inevitable in the moving world of IT) is well managed"
Buxted Construction
"The iSOS team helped us to create a database for our production company. The entire process from start to finish was very straightforward and they took great care to explain every step and worked very hard to give us a finished product which was tailor-made to our needs."
Freckle Productions
"“This was our first major FileMaker project. Working with iSOS has been a good collaborative experience, and the majority of the work has been done remotely. The benefit of a fully customised system is that we can continue to improve the way it works to precisely fit the needs of our business."
Learning Resources for Schools
"iSOS listened to our brief and our needs and were able to provide us with advice, suggestions as to how to structure the solution and eventually an accurate, detailed quote that didn’t change during the entire process. The solution was delivered on time and on budget."
Mountain Spaces
"Heritage Collective approached iSOS to develop a bespoke database system. We’ve been very pleased with the result and they’ve been a great team to work with. Methodical and approachable, they took the time to understand our business and encouraged regular engagement which led to a tailor-made product that hit the spot."
Heritage Collective
"I would like to say thank you for delivering such a great application so quickly and professionally. I was very impressed with the way that the team had gone through the documentation before the project brief, and had all of the right questions ready for us."
Eazy Collect
"Our experience through iSOS has been 5*, and the continued support from iSOS on very rare glitches (inevitable in the moving world of IT) is well managed"
Buxted Construction
"The iSOS team helped us to create a database for our production company. The entire process from start to finish was very straightforward and they took great care to explain every step and worked very hard to give us a finished product which was tailor-made to our needs."
Freckle Productions
"“This was our first major FileMaker project. Working with iSOS has been a good collaborative experience, and the majority of the work has been done remotely. The benefit of a fully customised system is that we can continue to improve the way it works to precisely fit the needs of our business."
Learning Resources for Schools
"iSOS listened to our brief and our needs and were able to provide us with advice, suggestions as to how to structure the solution and eventually an accurate, detailed quote that didn’t change during the entire process. The solution was delivered on time and on budget."
Mountain Spaces
"Heritage Collective approached iSOS to develop a bespoke database system. We’ve been very pleased with the result and they’ve been a great team to work with. Methodical and approachable, they took the time to understand our business and encouraged regular engagement which led to a tailor-made product that hit the spot."
Heritage Collective
"I would like to say thank you for delivering such a great application so quickly and professionally. I was very impressed with the way that the team had gone through the documentation before the project brief, and had all of the right questions ready for us."
Eazy Collect
"Our experience through iSOS has been 5*, and the continued support from iSOS on very rare glitches (inevitable in the moving world of IT) is well managed"
Buxted Construction
"The iSOS team helped us to create a database for our production company. The entire process from start to finish was very straightforward and they took great care to explain every step and worked very hard to give us a finished product which was tailor-made to our needs."
Freckle Productions
"“This was our first major FileMaker project. Working with iSOS has been a good collaborative experience, and the majority of the work has been done remotely. The benefit of a fully customised system is that we can continue to improve the way it works to precisely fit the needs of our business."
Learning Resources for Schools
"iSOS listened to our brief and our needs and were able to provide us with advice, suggestions as to how to structure the solution and eventually an accurate, detailed quote that didn’t change during the entire process. The solution was delivered on time and on budget."
Mountain Spaces
"Heritage Collective approached iSOS to develop a bespoke database system. We’ve been very pleased with the result and they’ve been a great team to work with. Methodical and approachable, they took the time to understand our business and encouraged regular engagement which led to a tailor-made product that hit the spot."
Heritage Collective
"I would like to say thank you for delivering such a great application so quickly and professionally. I was very impressed with the way that the team had gone through the documentation before the project brief, and had all of the right questions ready for us."
Eazy Collect
"Our experience through iSOS has been 5*, and the continued support from iSOS on very rare glitches (inevitable in the moving world of IT) is well managed"
Buxted Construction
"The iSOS team helped us to create a database for our production company. The entire process from start to finish was very straightforward and they took great care to explain every step and worked very hard to give us a finished product which was tailor-made to our needs."
Freckle Productions
"“This was our first major FileMaker project. Working with iSOS has been a good collaborative experience, and the majority of the work has been done remotely. The benefit of a fully customised system is that we can continue to improve the way it works to precisely fit the needs of our business."
Learning Resources for Schools
"iSOS listened to our brief and our needs and were able to provide us with advice, suggestions as to how to structure the solution and eventually an accurate, detailed quote that didn’t change during the entire process. The solution was delivered on time and on budget."
Mountain Spaces
"Heritage Collective approached iSOS to develop a bespoke database system. We’ve been very pleased with the result and they’ve been a great team to work with. Methodical and approachable, they took the time to understand our business and encouraged regular engagement which led to a tailor-made product that hit the spot."
Heritage Collective
"I would like to say thank you for delivering such a great application so quickly and professionally. I was very impressed with the way that the team had gone through the documentation before the project brief, and had all of the right questions ready for us."
Eazy Collect
"Our experience through iSOS has been 5*, and the continued support from iSOS on very rare glitches (inevitable in the moving world of IT) is well managed"
Buxted Construction
"The iSOS team helped us to create a database for our production company. The entire process from start to finish was very straightforward and they took great care to explain every step and worked very hard to give us a finished product which was tailor-made to our needs."
Freckle Productions
"“This was our first major FileMaker project. Working with iSOS has been a good collaborative experience, and the majority of the work has been done remotely. The benefit of a fully customised system is that we can continue to improve the way it works to precisely fit the needs of our business."
Learning Resources for Schools
"iSOS listened to our brief and our needs and were able to provide us with advice, suggestions as to how to structure the solution and eventually an accurate, detailed quote that didn’t change during the entire process. The solution was delivered on time and on budget."
Mountain Spaces
"Heritage Collective approached iSOS to develop a bespoke database system. We’ve been very pleased with the result and they’ve been a great team to work with. Methodical and approachable, they took the time to understand our business and encouraged regular engagement which led to a tailor-made product that hit the spot."
Heritage Collective
"I would like to say thank you for delivering such a great application so quickly and professionally. I was very impressed with the way that the team had gone through the documentation before the project brief, and had all of the right questions ready for us."
Eazy Collect
"Our experience through iSOS has been 5*, and the continued support from iSOS on very rare glitches (inevitable in the moving world of IT) is well managed"
Buxted Construction
"The iSOS team helped us to create a database for our production company. The entire process from start to finish was very straightforward and they took great care to explain every step and worked very hard to give us a finished product which was tailor-made to our needs."
Freckle Productions
"“This was our first major FileMaker project. Working with iSOS has been a good collaborative experience, and the majority of the work has been done remotely. The benefit of a fully customised system is that we can continue to improve the way it works to precisely fit the needs of our business."
Learning Resources for Schools
"iSOS listened to our brief and our needs and were able to provide us with advice, suggestions as to how to structure the solution and eventually an accurate, detailed quote that didn’t change during the entire process. The solution was delivered on time and on budget."
Mountain Spaces
"Heritage Collective approached iSOS to develop a bespoke database system. We’ve been very pleased with the result and they’ve been a great team to work with. Methodical and approachable, they took the time to understand our business and encouraged regular engagement which led to a tailor-made product that hit the spot."
Heritage Collective
"I would like to say thank you for delivering such a great application so quickly and professionally. I was very impressed with the way that the team had gone through the documentation before the project brief, and had all of the right questions ready for us."
Eazy Collect
"Our experience through iSOS has been 5*, and the continued support from iSOS on very rare glitches (inevitable in the moving world of IT) is well managed"
Buxted Construction
"The iSOS team helped us to create a database for our production company. The entire process from start to finish was very straightforward and they took great care to explain every step and worked very hard to give us a finished product which was tailor-made to our needs."
Freckle Productions
"“This was our first major FileMaker project. Working with iSOS has been a good collaborative experience, and the majority of the work has been done remotely. The benefit of a fully customised system is that we can continue to improve the way it works to precisely fit the needs of our business."
Learning Resources for Schools
"iSOS listened to our brief and our needs and were able to provide us with advice, suggestions as to how to structure the solution and eventually an accurate, detailed quote that didn’t change during the entire process. The solution was delivered on time and on budget."
Mountain Spaces
"Heritage Collective approached iSOS to develop a bespoke database system. We’ve been very pleased with the result and they’ve been a great team to work with. Methodical and approachable, they took the time to understand our business and encouraged regular engagement which led to a tailor-made product that hit the spot."
Heritage Collective
"I would like to say thank you for delivering such a great application so quickly and professionally. I was very impressed with the way that the team had gone through the documentation before the project brief, and had all of the right questions ready for us."
Eazy Collect
"Our experience through iSOS has been 5*, and the continued support from iSOS on very rare glitches (inevitable in the moving world of IT) is well managed"
Buxted Construction
"The iSOS team helped us to create a database for our production company. The entire process from start to finish was very straightforward and they took great care to explain every step and worked very hard to give us a finished product which was tailor-made to our needs."
Freckle Productions
"“This was our first major FileMaker project. Working with iSOS has been a good collaborative experience, and the majority of the work has been done remotely. The benefit of a fully customised system is that we can continue to improve the way it works to precisely fit the needs of our business."
Learning Resources for Schools
What We Do
Tech Solutions for Tomorrow
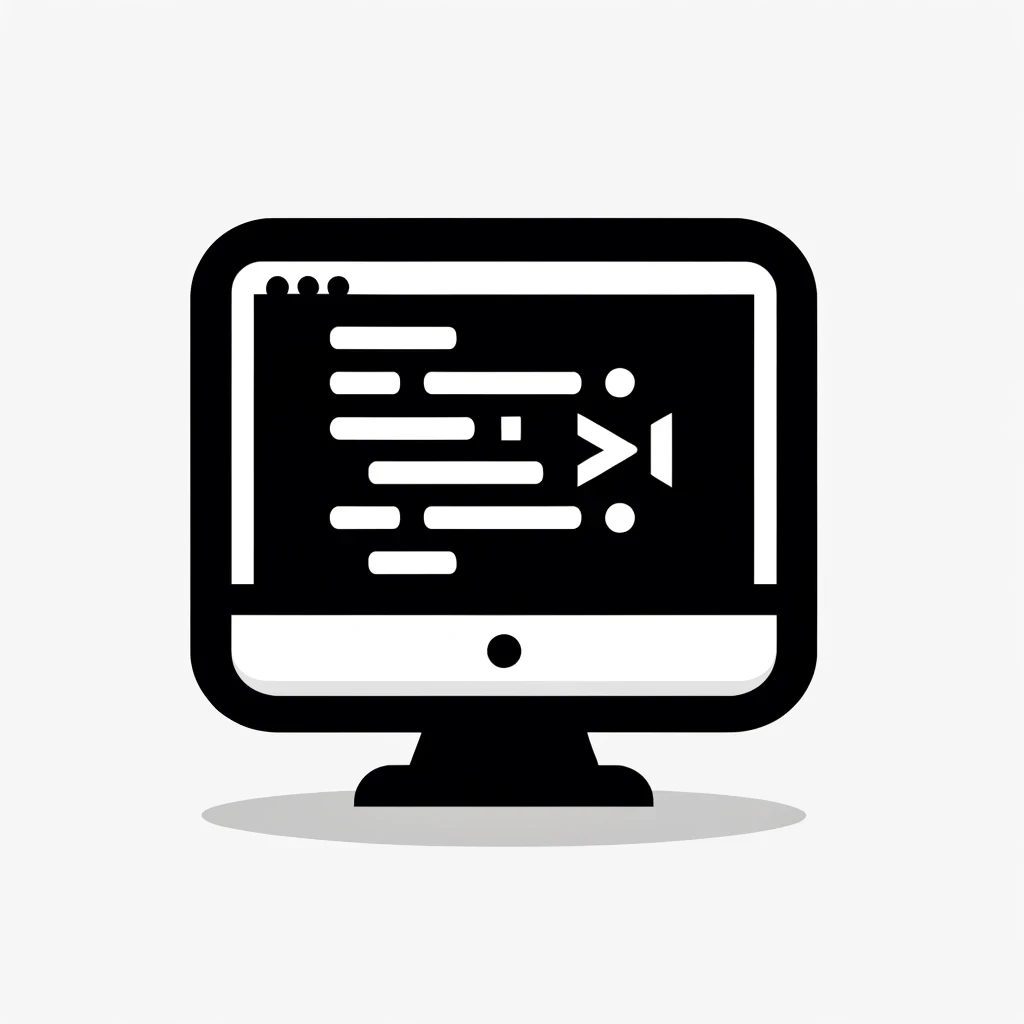
Web Development
Having a website is no longer enough. Your custom site must be easily found, engaging, and deliver a clear message.
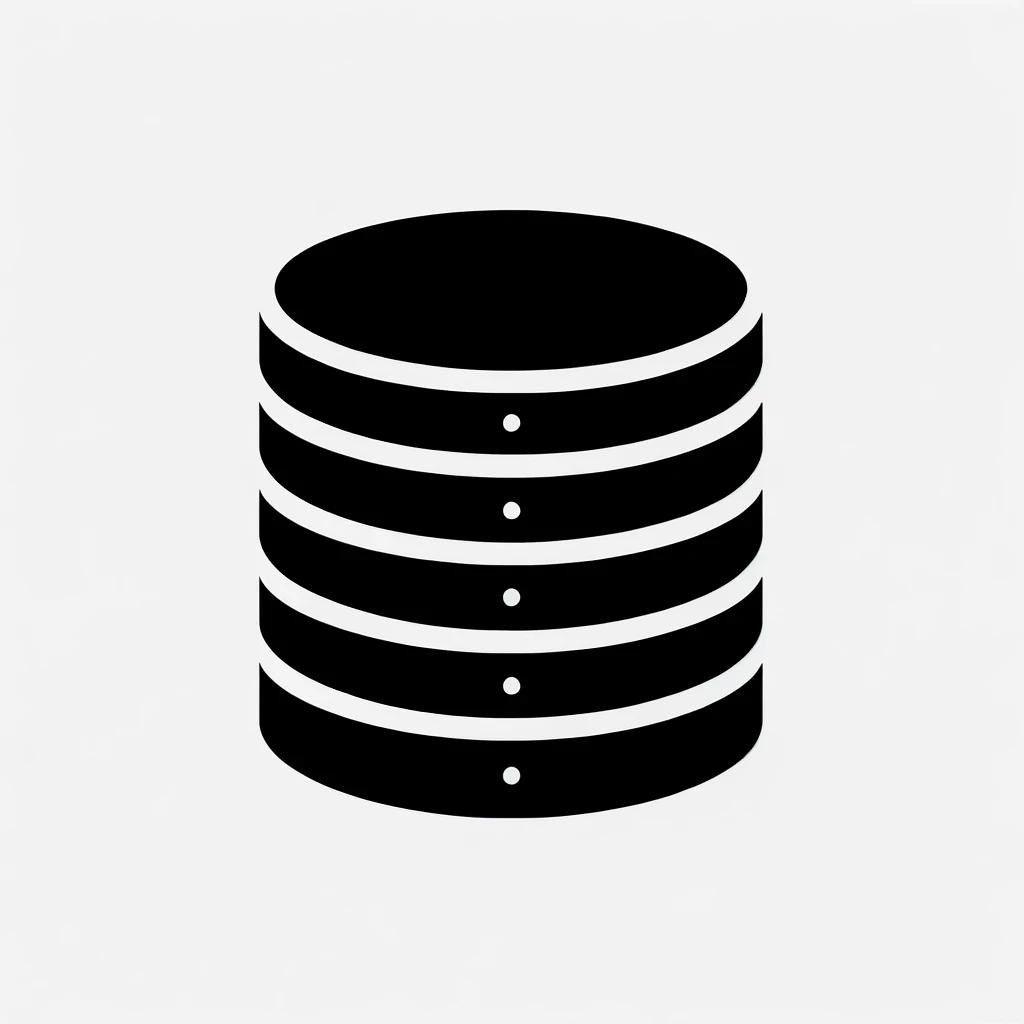
Claris Databases
With over 400 custom Claris FileMaker databases delivered in 10 years, iSOS understands why organisations invest in new database software.
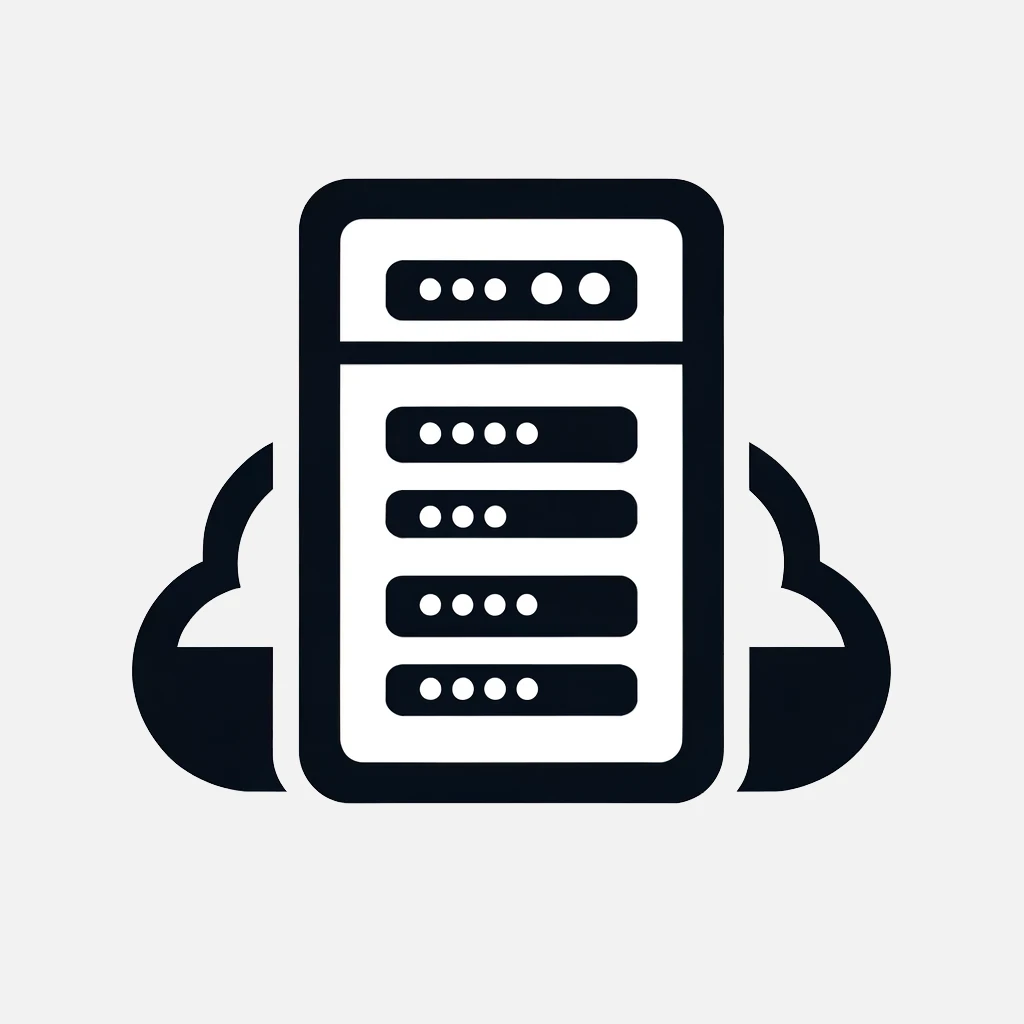
macOS & Windows Support
We offer expert macOS and Windows support, ensuring your systems run smoothly and efficiently.
Ready to Elevate Your Digital Presence?
Don't get left behind
Ensure your business stays ahead with cutting-edge digital solutions. Contact us today to keep your company at the forefront of your industry and continue thriving.
Stay Connected with iSOS
Copyright: © 2025 iSOS. All Rights Reserved.
What We Do
Tech Solutions for Tomorrow
Ready to Elevate Your Digital Presence?
Don't get left behind
Ensure your business stays ahead with cutting-edge digital solutions. Contact us today to keep your company at the forefront of your industry and continue thriving.
Stay Connected with iSOS
Copyright: © 2025 iSOS. All Rights Reserved.
What We Do
Tech Solutions for Tomorrow
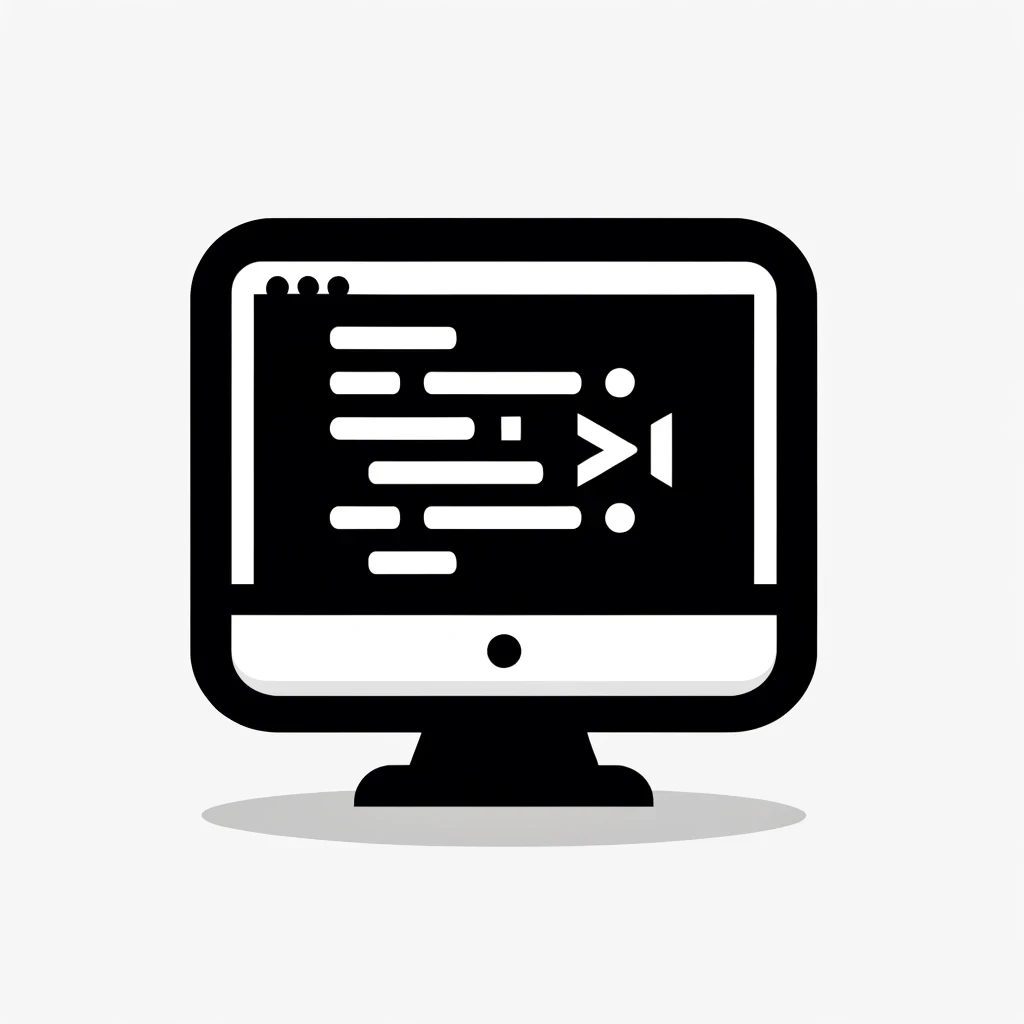
Web Development
Having a website is no longer enough. Your custom site must be easily found, engaging, and deliver a clear message.
Ready to Elevate Your Digital Presence?
Don't get left behind
Ensure your business stays ahead with cutting-edge digital solutions. Contact us today to keep your company at the forefront of your industry and continue thriving.
Stay Connected with iSOS
Copyright: © 2025 iSOS. All Rights Reserved.